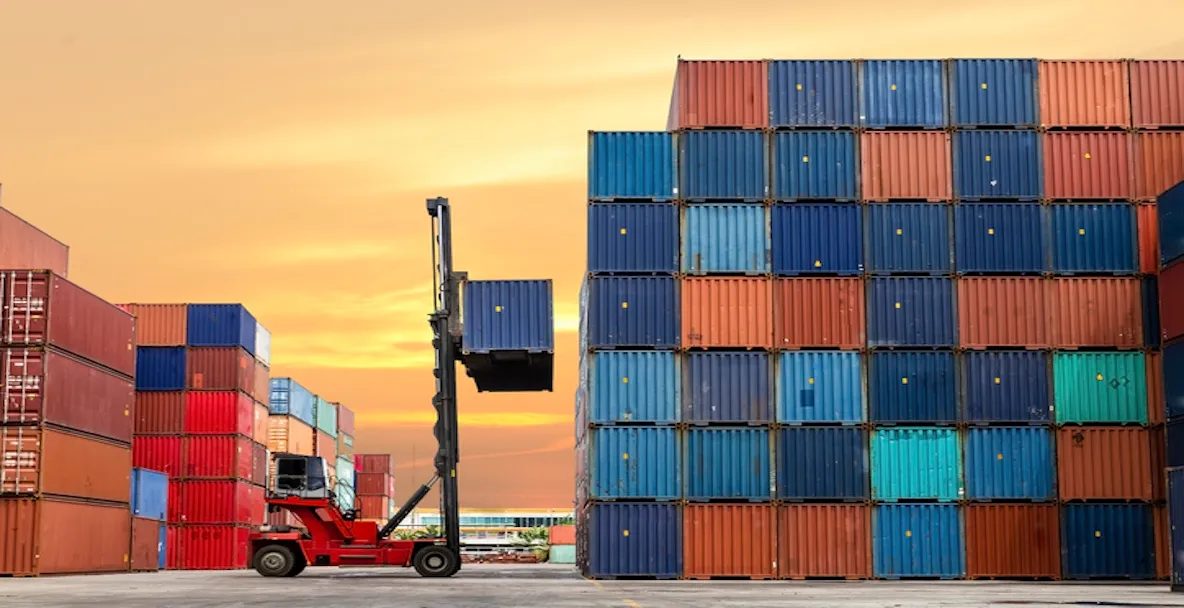
In the last several weeks, the global supply chain has been rocked by various challenges. Over the past year, there have been numerous disruptions that have been sufficiently mitigated by companies due to flat consumer demand and remaining excess inventory filling backlogs. That said, the globe faces an unprecedented increase in supply chain challenges from a confluence of geopolitical tensions and environmental disasters not seen since the early days of the COVID-19 pandemic.
Supply chain disruptions are not uncommon within modern globalization. The more widespread industries are, the greater the chance they will experience issues ranging from geopolitics to mother nature. Even market demand shifts can discombobulate the supply chain if suppliers and buyers aren’t prepared for sudden trends.
The semiconductor supply chain is particularly vulnerable to disruptions due to the high concentration of manufacturing and assembly facilities in one geopolitical area. The electronic components industry requires precise logistics, as the materials used to manufacture a single semiconductor must be handled delicately and transported rapidly, or the component risks degradation.
During the COVID-19 pandemic, many challenges occurred rapidly, which led to the monumental semiconductor shortage. Pandemic lockdowns, dramatic shifts in market demand, severe weather, and port congestion contributed to delays that exacerbated lead times and strained limited production capacity.
As these issues resolved, recession concerns triggered a market downturn making components far more accessible than they were a few months prior. The world then experienced a severe market downturn as companies were left with months of stock and no one to buy it.
The slowdown in the semiconductor market has significantly reduced lead times for certain parts. After the harsh slump the market experienced the year prior, demand has remained flat. This is why the current compounding of challenges over the last several weeks has not yet triggered the same blaring alarm bells experienced during the early days of the pandemic.
However, with the industry approaching the end of the year, holiday procurement and start-of-year buying are just around the corner. At the very least, these issues will take weeks to mitigate, which could lead to some shortages. Should the market pick up, this disruption may become so widespread that it triggers the same buying habits seen at the beginning of the global semiconductor shortage.
The U.S.-China Trade War: Escalating Tariffs and Export Controls
The trade war between the U.S. and China has been ongoing over the last several years but increased in severity once semiconductor accessibility became a primary focus for both governments. Each country excels in specific areas of the semiconductor supply chain, making each retaliatory response another hurdle that adds complexity to an already fragile supply chain.
The United States leads the world in advanced semiconductor design, with most of the world's leading chip designers based in the U.S. On the other hand, China is the primary supplier of several minerals essential in manufacturing semiconductors, including silicon, gallium, and germanium.
Over the last few years, the United States has banned the export of advanced semiconductors and chip manufacturing equipment to China. In response, China passed restrictions on exports of gallium and germanium. When the U.S. put stricter controls on AI-capable chips sold to China, China announced that American memory supplier Micron Technology had failed its security analysis--move largely viewed as retaliatory--and could no longer be sold to companies supporting critical infrastructure.
In the last few months, the U.S. has expanded its restricted list so that more components are included on its ban. Furthermore, the U.S. had announced its foreign direct product rule (FDPR), which would allow the U.S. to stop the sale of products created using American technology. This would impact companies like Samsung Electronics, which produces chips using American equipment but has not yet been affected by previous restrictions.
Likewise, the U.S., EU, and Canada have placed hefty tariffs on Chinese made electric vehicles, with the U.S. also enforcing a 25% tariff on Chinese minerals including steel, aluminum, unwrought tantalum, lithium-ion batteries, and more.
Heightened tension between the two countries has increased uncertainty for many companies as production and logistics costs rise.
Likewise, China’s push to develop its semiconductor industry could upheave the global supply chain, especially as countries try to reduce their dependence on each other. Industry analysts are concerned that Chinese companies could flood the market with an oversupply of cheap alternatives, drastically driving prices down.
Whether or not an increase in China-made chips comes to fruition, an argument that industry insiders have been debating since the start of the trade war, the increase in tariffs and restrictions has made it more complex for companies to get their hands on the chips they need. This is especially true for aerospace and defense organizations that require highly specialized legacy chips, of which China has plenty of.
Typhoons Gaemi and Yagi: The Supply Chain’s Vulnerability to Natural Disasters
2023 was a historic year for billion-dollar weather events, and 2024 is following in its footsteps. The global semiconductor supply chain started the year off with a devastating earthquake in Japan and a drought in the Panama Canal. There has been a rise in billion-dollar weather events over the last decade, with severe storms, droughts, wildfires, and other disasters significantly damaging local communities and facilities.
Over the years, the semiconductor supply chain has mitigated the impact of these natural disasters through strict preparedness systems, which was seen during the Hualien earthquake. As the largest producer of semiconductors, Taiwan, home to dozens of chip facilities, saw a limited impact on the supply chain after the strongest earthquake in the country’s last 25 years rocked its foundation.
However, many of these challenges, the earthquakes and drought, occurred weeks apart, giving the industry time to adjust and assess the damage.
Within the last month, Southeast Asia has been rocked by a deadly typhoon season, with Typhoon Gaemi and Super Typhoon Yagi greatly affecting several countries. Gaemi was the most severe typhoon to hit the semiconductor industry epicenter of Taiwan in eight years. TSMC, the crown jewel of the semiconductor industry, came out relatively unscathed thanks to its disaster preparedness.
Unfortunately, many other facilities did not experience the same outcome. Severe flooding submerged many parts of Vietnam and Thailand, with farms and villages struggling to cope with the looming possibility of landslides. In Vietnam, Yagi struck the Red River Delta, which is home to critical economic hubs “such as Hanoi and Hai Phong, as well as the provinces of Quang Ninh, Bac Ninh, Bac Giang, and Thai Nguyen. These areas collectively contribute 38% of Vietnam’s GDP and 55% of its export revenue.”
Many factories within the typhoon’s path have been flooded, resulting in damaged inventory, power outages, roof damage, structural collapse, and road erosion.
According to a report by CEL, 72.7% of companies experiencing supply chain and logistics disruptions are port operators, third-party logistics (3PL), last-mile delivery companies, and cold chain service companies. The concentrated impact in North Vietnam has amplified disruptions across critical logistics hubs in an area working its way back after the disastrous effects of Typhoon Gaemi.
These typhoon-related power outages, transportation delays, and factory shutdowns have significantly increased port congestion across the Southeast Asian supply chain. Due to the damaged transportation infrastructure around the area, lead times could see increased delays ranging from days or weeks. The port strikes in the East and Gulf Coasts of the United States had the potential to further exacerbate the situation had a tentative deal not been struck.
ILA Port Strikes: Danger Averted for Now
The International Longshoremen’s Association (ILA) port strikes along the U.S. East and Gulf Coasts had the potential to complicate pre-existing supply chain challenges for semiconductor manufacturers. Major ports, including those in Baltimore, Houston, and New York, handle vast quantities of goods, including semiconductors. According to Maersk, a week of strikes could have created backlogs that would take 4 to 6 weeks to resolve.
The strike reached a tentative deal on Friday, putting an “end to the biggest work stoppage of its kind in nearly half a century, which blocked unloading of container ships from Maine to Texas and threatened shortages of everything from bananas to auto parts, triggering a backlog of anchored ships outside major ports.”
With a tentative deal in place, this hopefully ended the concerning effect on industry-wide price increases and delayed lead times. However, the deal only keeps the ILA from striking until January, at which they will resume unless future negotiatiojns are successful.
“Port closures would not initially raise consumer prices because companies recently accelerated shipments of key goods. However, a prolonged stoppage would have eventually filtered through, with food prices likely to react first,” according to Morgan Stanley economists.
This came when port congestion was already rising due to the typhoons in Asia and the rising urgency to send out shipments ahead of time to avoid strikes. Likewise, the impact of Hurricane Helene in the Southern U.S. had only further heightened the need for reliable transportation of goods to those in the areas affected by the hurricane.
Hurricane Helene and the Impact on Spruce Pine Quartz Mining
Helene was a Category 4 hurricane that left dozens of communities in several states without power, water, and medical supplies. Like the deadly typhoons in Asia, the destruction has been nothing short of cataclysmic, leaving hundreds dead and some towns wiped off the map entirely. As authorities and volunteers help deliver aid to stranded survivors and clear roads for emergency vehicles, there is a growing concern over the fate of the mining operations in North Carolina’s small region of Spruce Pine.
As the world’s leading supplier of highly pure quality quartz, Spruce Pine supplies most of the semiconductor industry, with the minerals it needs to fabricate silicon wafers.
"Spruce Pine was drenched by 600 millimeters of rain from Tuesday to Saturday,” reported the Associated Press. The torrential rain and wind from Helene have washed out roads and damaged railways in the area, leaving most of the buildings within the region without power.
“Our dedicated teams are on-site, conducting cleanup and repair activities to restart operations as soon as we can,” Sibelco wrote in an update Friday. The Belgian company added the power remains out at its Western North Carolina mines but that repairs have “progressed significantly.”
On Friday, the company reported that its final product stock “has not been impacted” by the storm. “We are working closely with our customers to assess their needs and plan the restart of product shipments as soon as we can,” Sibelco said.
Quartz Corp., another company operating in the Spruce Pine mine, has yet to determine when operations will recommence and is prioritizing its workers' health and safety before addressing mining operations.
Even if either company can quickly repair the minor damage, there is still a problem getting shipments out of the region. Transportation has become severely limited due to the extensive damage done to the roads and railways, meaning there will be a disruption in getting supplies out. How significantly this will impact the semiconductor supply chain depends on how long the disruptions endure.
A fire at Spruce Pine in 2008 sent shifters down the semiconductor supply chain. Suppose this disruption lasts more than a few weeks. In that case, Johannes Bernreuter, Head of Bernreuter Research, says it “would pose a significant problem for producing silicon ingots needed in the photovoltaic, or PV, industry.”
Without any immediate viable sources to utilize in place of North Carolina, there will be a delay in availability that will directly affect the entire silicon supply chain, leading to potential shortages. Compounded with port congestion from typhoons and the hurricane, lead times could be delayed significantly as the semiconductor industry prepares for re-emerging demand in 4Q24 and 1Q25.
Hurricane Milton, which is rolling in only 10 days after Helene, has the potential to amplify these damages.
“This is it, folks,” said Cathie Perkins, Emergency Management Director in Pinellas County. “Those of you who were punched during Hurricane Helene, this is going to be a knockout. You need to get out, and you need to get out now.
The Compound Effect on the Semiconductor Supply Chain
These geopolitical, environmental, and labor-related issues can create ripples across the semiconductor supply chain. When combined, they form a perfect storm of disruptions, leading to increased lead times, rising costs, and uncertain production schedules that affect original equipment manufacturers (OEMs), contract manufacturers (CMs), and electronic manufacturing service (EMS) providers of all sizes.
So far, the effects have been muted due to flat consumer demand, which keeps lead times low across most markets. Backlogs that arise are filled with excess inventory that hasn’t yet been digested or mitigated. However, the meteoric rise in artificial intelligence has led to shortages in certain products over the years, and the AI market is only expected to continue seeing high demand. That requires uninterrupted logistics and a steady supply of raw materials like high-quality quartz.
Like the start of the global semiconductor shortage, a perfect storm of disruptions compounding together can lead to massive consequences for the semiconductor industry. Governments worldwide have been working hard to help revitalize domestic efforts through initiatives like the CHIPS Act. However, greater diversification of sources involving domestic and foreign suppliers can help protect against many challenges.
To prepare for a perfect storm of disruptions like the one we face now, it is pertinent to partner with a global electronics component distributor that can ship anywhere, utilize robust data-driven tech tools, diversify your supplier sources, and partner with sourcing experts that can procure hard-to-find components ahead of time. The industry needs to shift from reactive approaches to proactive ones to remain in control no matter what issue arises.
Recovery in a Time of Uncertainty
While the semiconductor industry has long been accustomed to navigating disruptions, the combination of geopolitical tensions, natural disasters, and labor strikes poses an unprecedented challenge. Recovery from these disruptions will depend on adaptability and collaboration to mitigate the worst effects. Building more resilient, diversified supply chains will be crucial to ensuring the stability of the global semiconductor market in the years to come.
It is necessary to partner with a global electronic components distributor well-versed in supply chain challenges and equipped with the solutions to combat them. Sourceability and its e-commerce platform, Sourcengine, can help organizations obtain the stock they need no matter what disruption impacts the supply chain.
Through franchise partnerships and a global team of procurement experts, Sourceability can help organizations obtain the needed stock or sell off excess inventory before it racks up thousands in additional costs. Through years of historical supply chain data, Sourceability can help organizations become aware of components that are more at risk of disruptions through its market intelligence tool, Datalynq.
Combined with Sourcengine, OEMs, CMs, and EMS providers can form a more robust, disruption-resilient supply chain while having industry experts provide solutions at every step. Sourceability can help you overcome these recent challenges and others appearing in the following weeks. Contact us here to get started leveraging our cutting-edge solutions and experienced team.
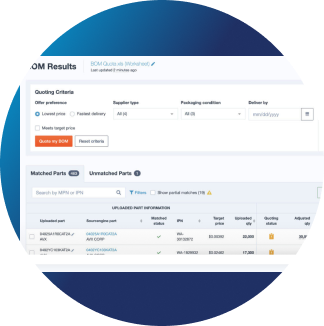
Quotengine: Your Ultimate BOM Tool
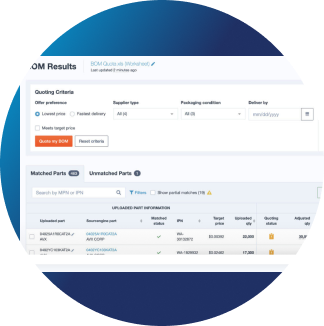
What’s Your Excess Worth?
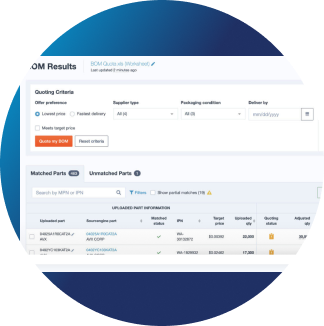
The Last Integration You’ll Ever Need
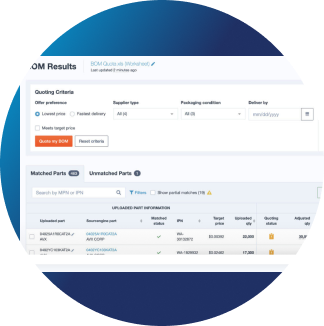
Sourcengine’s Lead Time Report
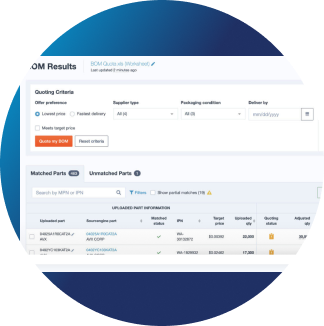
Sourcengine’s Lead Time Report
Your Lead Time Overview
Subscribe HereStruggling with excess inventory?
Download your free copy!.png)