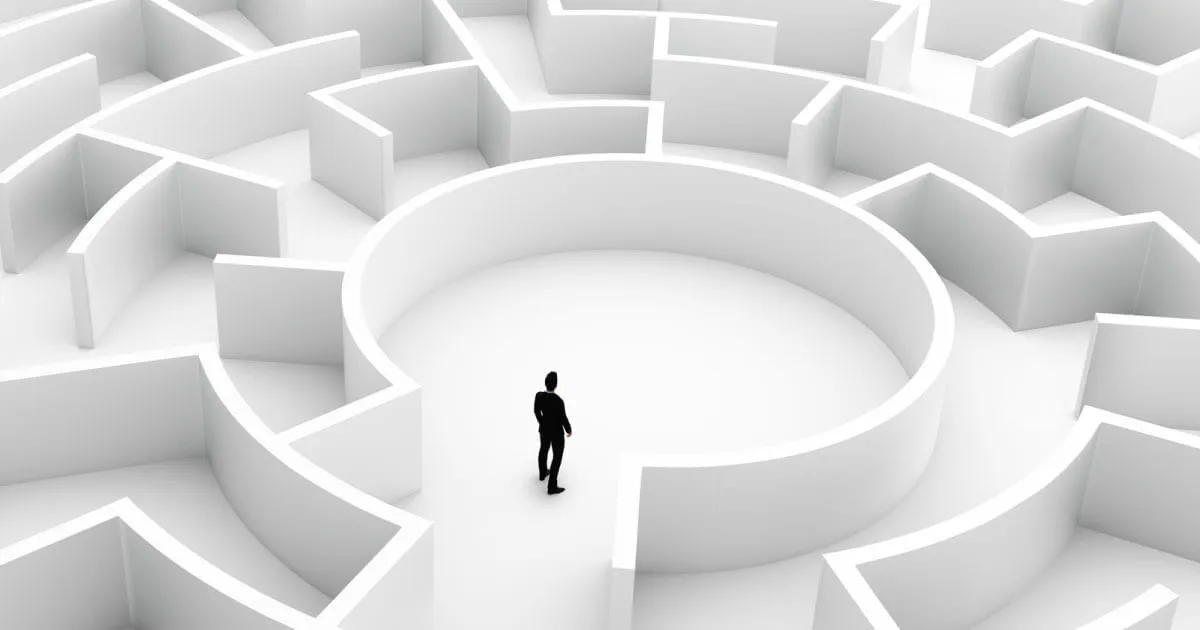
The hardships brought on by 2020 have been historic, and communities have felt these challenges on a global scale. However, there have been beacons of hope strewn throughout the disarray. Within the components industry, specifically, this year showed us the resilience and resourcefulness of many companies.
Faced with an economic downturn, a rapidly spreading virus, production demands, and more, companies were forced to pivot in a truly fluid situation that continues to evolve daily. Many organizations were able to shift production focus and bail out the struggling healthcare industry, burdened by the demand of COVID-19 cases and a dire shortage of medical supplies.
This year has also displayed the fragile nature of supply chains. It seems the fabric that connects the global economy is exceedingly thin, and the pandemic has shined a light on these shortcomings that, until now, many companies overlooked.
The fragility of the system becomes more clear when considering the heavy reliance on China and the nation's multitude of global relationships. These relationships were put on hold as countries around the world had to temporarily isolate themselves to combat the virus.
To make matters worse, Wuhan, ground zero for the outbreak, is a global semiconductor and mechanical hub that connects China with companies across the world. According to a study published by Dun & Bradstreet, 51,000 companies have at least one direct or Tier 1 supplier from China. Additionally, five million companies have Tier 2 suppliers in the nation. Those are staggering figures. It goes without saying that China is an integral cog in global supply chains.
We were given a hard look at the shortcomings of the system as we knew it. Now companies must mitigate risk and overhaul procedures that were previously thought to be ironclad.
There is another positive takeaway of 2020. This year presented companies with a valuable opportunity to learn from the mistakes that rocked global supply chains. For example, an absence of diversification, reluctance to adopt new technologies, and a convoluted trucking industry led to tie-ups and, ultimately, broken links in an already shaky chain.
The good news is that the situation is already improving. As of this writing, organizations are already shifting strategies and developing contingencies to shore up any vulnerabilities exploited by the unprecedented challenges posed by the pandemic.
With the future already looking bright, here's how supply chains can adapt to the new normal.
Look Beyond the Surface Level of Supply Chains
As supply chains began to fold, it became increasingly clear that many companies only held surface level comprehension of an otherwise complex concept. Safety nets were not in place, lead times skyrocketed, and entire supply chains eventually collapsed under the stress.
Understanding the complex and nuanced ways in which supply chains operate requires more than a superficial understanding, but a deep dive into each thread that comprises the tapestry. A key challenge in 2021 will be for companies to evolve in their thinking and use of technology when it come to the supply chain.
Expand the Supply Chain Horizon
While relying on one production source is a cost-effective, efficient tactic that once sufficed, the pandemic exposed the weakness in this philosophy. Companies depending on one production source had nowhere else to turn when the fast-spreading virus severed contact with suppliers.
As a safety net, companies should seek to diversify their sources. Though that path can be cost-prohibitive, companies will be able to avoid the worst-case scenarios of being shut off by their sole suppliers. There are worse things at stake than digging a bit deeper into company coffers. (See the aforementioned Dun & Bradstreet study above.)
Lean More on AI
From cars to healthcare and everything in between, societies continue to lean on AI. And the global economy is no different. In fact, AI is projected to contribute over $15 trillion to the global economy in the next decade. Supply chains, too, continue to integrate AI into their model.
As supply chains continue to adopt AI, the inherent risk of human error is reduced. AI also analyzes data, extrapolates that data, and determines how to best increase efficiency. In short, AI is tailor-made for integration into supply chains, and companies would be remiss not to leverage that. Look for more organizations to implement AI into 2021 and beyond.
Internet of Things (IoT) and Data
Speaking of leveraging AI and their resultant data, the Internet of Things (IoT) has the potential to generate a wealth of data. Automating processes with IoT not only increases efficiency; it can provide mountains of data from which companies can continue to adapt their strategies and learn.
IoT is currently in use in fields like logistics and aerospace. As companies continue to plan for the future, we should see even wider use of IoT in the components sector. As companies continue to implement IoT in their operations, key operational data is yielded. If these companies do not want to be left behind, implementing IoT will be a priority.
Simplify Haulage Strategies
Trucking goods domestically is a crucial part of transportation in supply chain models. In fact, trucking accounts for roughly 70 percent of domestic freight transport in the U.S., according to the American Trucking Associations.
However, this dependence on trucking comes with a caveat. The trucking sector remains overwhelmingly convoluted. Rather than a centralized model, with one or even a handful of companies offering to transport goods, there remains an extensive amount of individual companies that suppliers must wade through. This obfuscation can jam up the process, reduce efficiency, and lead to further complicated matters.
If companies are to continue to evolve and streamline operations into the future, smoothing out this complicated process and finding efficient pathways in a decentralized trucking industry should be a top priority.
Preparing for the Future
Yes, 2020 has been a challenging year, and supply chains have been flipped upside down as a result. But these hardships have also provided companies with a priceless blueprint on how to avoid future supply chain disasters.
By diversifying operations, adopting new technology, leveraging resultant data from the technology, and reinforcing supply chains, companies can prepare for a much brighter 2021.
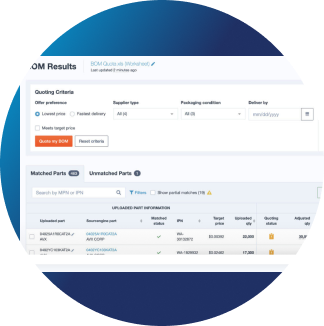
Quotengine: Your Ultimate BOM Tool
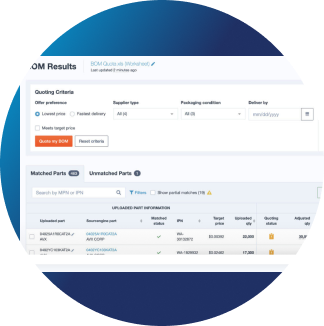
What’s Your Excess Worth?
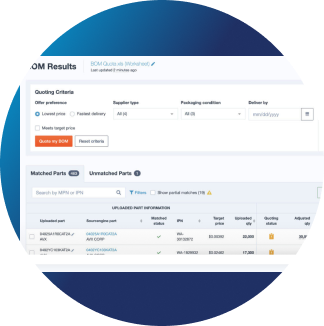
The Last Integration You’ll Ever Need
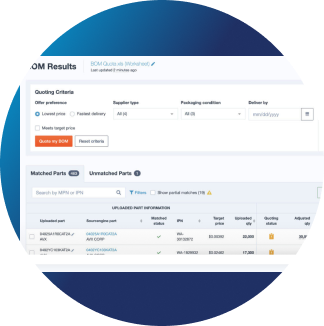
Sourcengine’s Lead Time Report
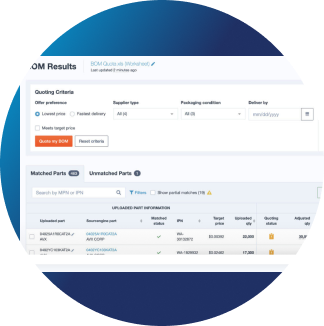
Sourcengine’s Lead Time Report
Your Lead Time Overview
Subscribe HereStruggling with excess inventory?
Download your free copy!.png)