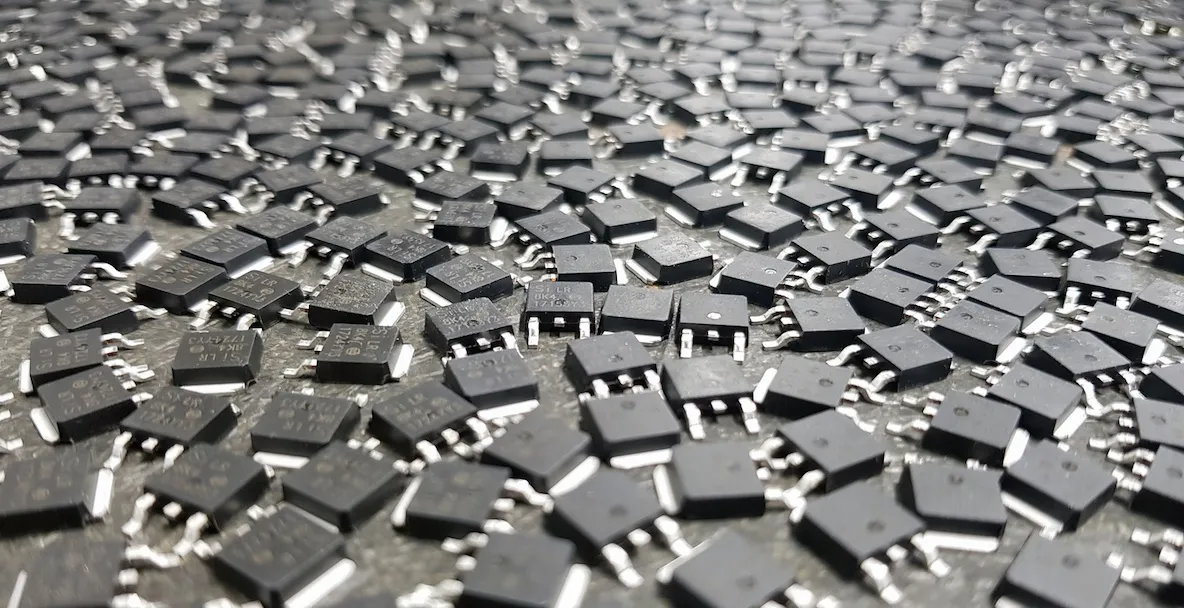
Over the last several years, access to electronic components has been catapulted into national headlines. As society sees the integration of advanced technologies grow by the year via applications like artificial intelligence (AI), 5G, and the Internet of Things (IoT), the need for a reliable stream of electronic components is pertinent to any nation’s economy and security.
This heightened attention truly kicked off during the global semiconductor shortage between 2020 and 2022. The Covid-19 pandemic lit the match, demand for electronic components exploding as remote work took off. As vaccines were developed and lockdowns eased, automakers saw a tidal wave of orders, further exacerbating the strained supply chain.
Capacity constraints due to lockdowns, natural disasters, and high market demand contributed to many original equipment manufacturers (OEMs), contract manufacturers (CMs), and electronic manufacturing service (EMS) providers engaging in double-ordering. Double-ordering is placing two of the same order to increase inventory and protect against future shortages by ensuring "safety stock.” However, some organizations would cancel the second order whenever the first arrived, increasing the likelihood of excess inventory occurring through inflated demand.
Eventually, the market shifted as employees began returning to work, and the need for consumer electronics fell. What happened was a bullwhip from shortage to glut.
Excess electronic component inventory levels skyrocketed. Over 2023, many OEMs, CMs, and EMS providers were stuck with up to six months of inventory and no demand to digest it. Unlike other organizations, excess electronic component inventory cannot sit for long, depending on the component type. Many advanced semiconductors only have a lifespan of a few years, and that’s only if they are correctly stored in monitored conditions where components are not affected by electrostatic discharge (ESD), temperature, humidity, and other factors.
If not, they will degrade quickly, becoming unusable and further draining an organization’s capital.
Excess electronic component inventory is a significant challenge for OEMs, CMs, EMS providers, and even original component manufacturers (OCMs). It is essential to understand its causes, the risks associated with excess, and the steps to prevent its occurrence.
The Causes of Excess Inventory
The recent explosion in excess inventory was due to a perfect storm of contributing factors, including market volatility, supply chain disruptions, and inaccurate demand forecasting.
Market Volatility: The semiconductor industry often faces periods of high demand followed by quick and brutal downturns. The memory market, specifically DRAM and NAND flash, is prone to these cyclical ups and downs, as was seen during the semiconductor shortage and resulting glut. Economic slowdowns, customer demand shifts, and technological advances can quickly shift market trends, resulting in excess inventory when orders rapidly dry up.
Supply Chain Disruptions: The Covid-19 pandemic and following natural disasters, such as winter weather and earthquakes, resulted in significant disruptions that caused global supply chain bottlenecks. This constrained capacity quickly evolved into a worldwide shortage that prompted many OEMs, CMs, and EMS providers to double order to try and circumvent long lead times. This contributed to a massive overstock issue once supply chain conditions stabilized, and the component stock was more widely available. This can happen during any disruption, including geopolitical tension or obsolescence.
Inaccurate Demand Forecasts: In the electronic components industry, OCMs typically fill production capacity based on demand levels from the prior year with some room for adjustment. However, even minor inaccuracies can contribute to overproduction or underproduction. This was seen during the global semiconductor shortage, when automakers canceled orders at the start of the pandemic. However, when demand returned at the end of the year, OCMs had already reassigned capacity toward lucrative lines, leaving automakers scrambling for stock. In comparison, advanced semiconductors saw a significant rise in excess inventory when demand suddenly dropped off near the end of the year.
These factors can result in excess inventory, and when combined, they exacerbate the problem, leading to months of surplus organizations struggle with. Even now, as 2024 nears its end, the global electronic components industry is still dealing with areas of excess. Demand hasn’t fully returned despite bottlenecks for some components frequently used in artificial intelligence.
Efforts to mitigate excess electronic component inventory have been ongoing, and for good reason. Excess inventory can have a severe impact on an organization the longer it sits.
The Impact Excess Inventory Has on Organizations
The most significant problem that electronic component excess can have on OEMs, CMs, or EMS providers is financial. However, there are additional challenges that surplus stock can contribute to, further damaging a company’s operations.
- Increased Capital Spending: The most notable impact of excess inventory is increased capital spending on storing, insuring, and managing surplus stock when it could be used elsewhere. Electronic components require specialized storage that prevents components from deteriorating due to issues, such as ESD, humidity, and temperature. These allocated resources can add up over time, resulting in a significant amount of lost capital an organization can have prioritized elsewhere.
- Higher Obsolescence Risk: Technology is evolving rapidly, especially with the rise of generative AI. The rate of components entering obsolescence, or even instant obsolescence, is increasing because of the prioritization of lucrative lines during the semiconductor shortage. Unsold inventory that becomes obsolete can quickly lose value, exacerbating financial losses such as the additional costs used to store the excess inventory safely.
- Operational Inefficiency: Excess inventory requires management to store, maintain, dispose of, and repurpose it. This can slow down business operations as time is spent managing warehouses and staff or finding proper avenues to dispose of large quantities of electronic waste. This raises costs and strains company staff, who cannot focus on more significant priorities.
- Price Erosion: The more extended companies hold on to their excess inventory, the more likely the market value of these components will erode. This was seen during the semiconductor shortage when components were bought at massive price hikes compared to their typical sales price. These components' average selling prices (ASPs) are now significantly lower compared to shortage or typical market conditions. This dramatically impacts profitability, as companies sell excess at a discount rather than what they originally paid.
Excess electronic component inventory can be a detriment to OEMs, CMs, or EMS providers of any size. It is better to avoid excess inventory and have a plan to mitigate it as soon as possible, should it occur. Proactively preparing to avoid excess occurrences and creating a robust excess management plan is necessary to prevent these negative impacts.
3 Strategies for Managing Excess Inventory
To successfully manage excess inventory, no matter how severe, requires a multi-faceted approach. Companies should adopt a strategy that combines data analytics with stringent excess inventory management. Here are three essential steps that an organization should take to avoid and mitigate excess inventory:
1. Leveraging Data-Driven Insights to Monitor the Market
Demand prediction can be difficult for OEMs, CMs, and EMS providers, especially in an industry where the market can shift quickly, and it takes time for OCMs to ramp up production capacity. Using artificial intelligence and machine learning to discover insights into market behavior can help improve forecast predictability with more accurate estimates. This can help OEMs, CMs, and EMS providers know when to slow down or ramp up procurement efforts. It can also help identify components that may be more prone to disruptions, assisting organizations to prepare for supply chain disruptions or mitigate these challenges by removing risky components from their BOM list entirely. This helps reduce the likelihood of excess inventory or lessen the excess a company may be saddled with.
2. Using Digital Tools to Remove Risks and Optimize Inventory
There are specialized software tools that can help companies optimize their inventory levels based on real-time demand, lead times, and market conditions. These tools offer insights into how much available stock is on hand by different suppliers and can illuminate opportunities for when companies should begin to reorder or hold off. These tools can be integrated into a company’s enterprise resource planning (ERP) system to help streamline procurement through scheduled deliveries, so organizations don’t get caught up in double-ordering if lead times increase. These tools can also help companies become aware of risky components, like sole sources, and help design engineers and buyers find a more accessible form-fit-function (FFF) alternate or drop-in replacement (DIR). This can prevent risky buying practices contributing to excess inventory.
3. Collaboration with Distributors to Sell Inventory
Sometimes, excess inventory can happen despite a company’s best efforts. That is why OEMs, CMs, and EMS providers should partner with a global electronic components distributor. A global distributor often has the means to sell excess inventory at a reasonable price so that companies can recoup lost capital before additional costs add up. Distributors can help organizations mitigate excess inventory by leveraging their large audience of interested buyers to sell excess components. This allows buyers and sellers to reduce the risk of counterfeit components that enter the supply chain and the waste that can accumulate should excess inventory expire while stored.
These three strategies can help mitigate excess inventory before it becomes a problem. However, small OEMs, CMs, and EMS providers might not have the resources to invest in developing such digital tools. Luckily, there are some electronic component distributors that can accomplish all of the above and more.
Avoid Excess by Working with a Distributor that Handles Everything
Excess inventory is a problem the semiconductor industry will constantly face unless organizations adopt strategic approaches to lessen its occurrence and severity. Companies can circumvent the negative impacts by partnering with an electronic component distributor offering advanced digital tools to provide accurate market monitoring and excess management programs.
Sourceability’s global e-commerce platform, Sourcengine, helps organizations quickly sell their excess inventory through three different selling models to its audience of over 100,000 buyers. OEMs, CMs, and EMS providers interested in selling their excess stock can contact one of our experts worldwide to get started. Similarly, Sourcengine’s API platform can be integrated into any company’s ERP system to streamline procurement and schedule deliveries to ensure no double-ordering occurs when lead times are long.
Sourceability’s market intelligence platform, Datalynq, leverages Sourcengine’s historical market data to identify components that are more at risk of market shifts. Using Datalynq and Sourcengine, companies can be proactive in mitigating excess electronic component inventory and selling it off before it becomes a financial drain.
Excess inventory from 2023 is still a problem for some areas of the electronic component market. Contact our experts today if you're ready to sell your excess inventory.
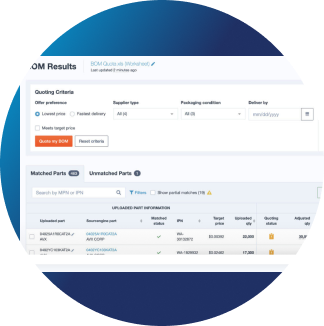
Quotengine: Your Ultimate BOM Tool
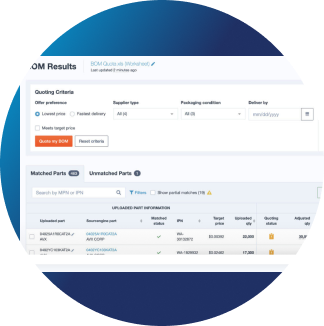
What’s Your Excess Worth?
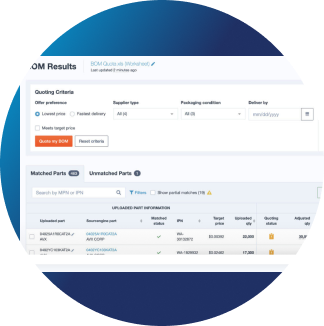
The Last Integration You’ll Ever Need
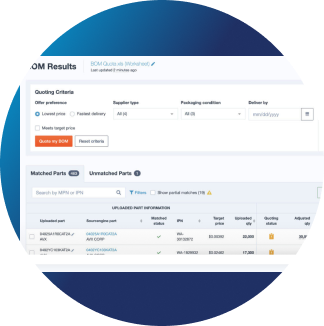
Sourcengine’s Lead Time Report
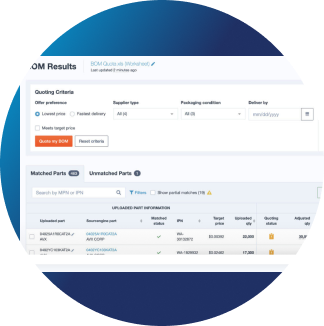
Sourcengine’s Lead Time Report
Your Lead Time Overview
Subscribe HereStruggling with excess inventory?
Download your free copy!.png)