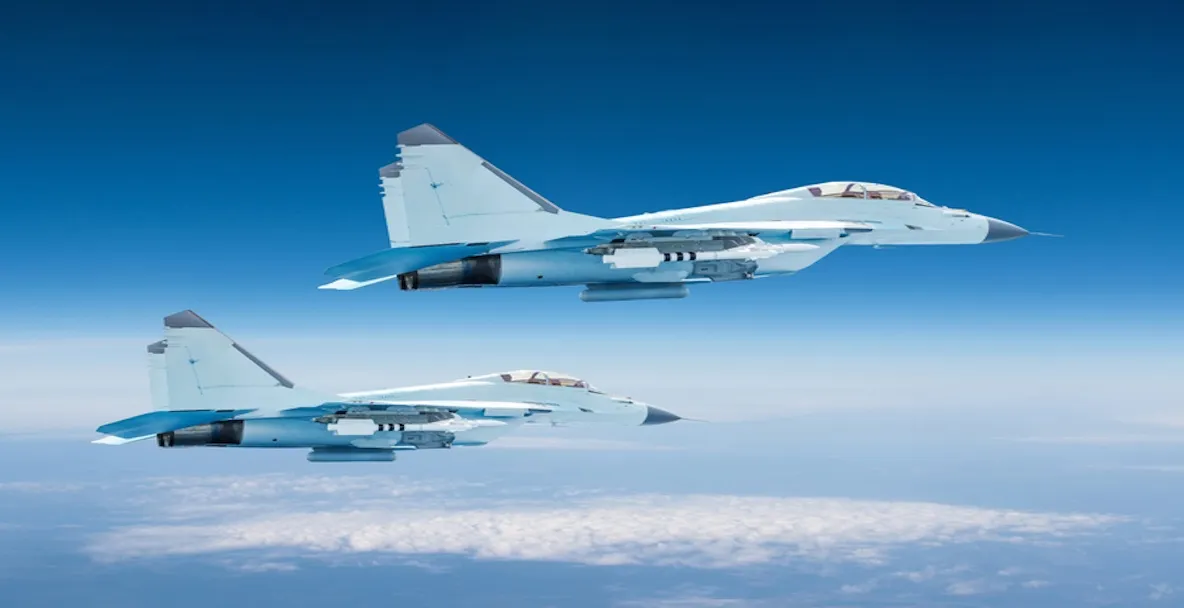
Since 2018, the U.S. and China have been engaged in an ongoing trade war that has had far-reaching economic effects on various markets. Due to increasing tensions, semiconductors have been subjected to numerous export limitations or bans between the two countries. The reason chips have taken center stage in this geopolitical conflict is due to the role they play in a country’s economic success and national security.
Semiconductors have become the backbone of modern society, shaping the global supply chain. Rising geopolitical volatility between the United States and China has led to a decoupling of that chain, disrupting chip accessibility as countries begin to safeguard their supplies while establishing new domestic facilities.
This had wide-reaching effects on numerous industries and countries. For decades, the semiconductor supply chain has been severely lacking in geopolitical diversity, with design, fabrication, and assembly and packaging being found in one specific location. For the United States, outsourcing semiconductor manufacturing to Southeast Asia has been the norm since the late 1990s. The United States has instead become a leader in semiconductor design and development, excelling in the creation of advanced semiconductors.
While Taiwan is arguably the king of semiconductor manufacturing, with TSMC producing over 50% of the world’s semiconductors and 90% of all advanced chips, China supplies the raw materials necessary for semiconductor fabrication alongside the production of older generation chips. These legacy components have fallen out of favor with consumer electronics manufacturers but are still regularly used in automotive, medical, aerospace, and defense industries.
Aerospace and defense industries are pertinent in maintaining and improving a country’s national security. To continue implementing more efficient measures, there must be a stable flow of authentic and readily available electronic components. While the United States has found it easy to restrict advanced components, its lack of a domestic supply chain that produces legacy components needed within the aerospace and defense industries puts its national security at risk.
Background of the U.S.-China Semiconductor Trade War
In 2018, the U.S. began imposing tariffs on Chinese goods due to concerns about “unfair trade practices, intellectual property theft, and national security risks,” as stated by the then-Trump Administration.
In response, Beijing imposed tariffs on American goods while declaring the U.S. tariffs were an act of “nationalist protectionism.”
In the following years, the trade war continued to escalate, despite the U.S. administration change from Trump to Biden and even amid the COVID-19 pandemic. By the end of the Trump Administration, many had characterized the trade war as a “failure,” but the Biden Administration kept the tariffs in place and continued to impose further restrictions.
In the last two years, the trade war that was once deemed a failure has heightened in intensity, with semiconductors, chip manufacturing equipment, and the raw minerals required to produce electronic components becoming the main subject of restrictions between either country. The U.S. and its dominant position in the design and intellectual property (IP) of semiconductors have greatly limited China’s domestic chip ambitions.
U.S. allies have followed suit in imposing bans or hefty tariffs on components and equipment, such as the Netherlands, which has kept the leading advanced lithography equipment manufacturer, ASML, from selling to Chinese companies. Without access to ASML’s equipment, Chinese companies have been racing to develop their own lithography equipment. This massive task will likely take years. After all, it took ASML decades to develop their current manufacturing equipment.
In response to these restrictions, China has placed export limitations on critical minerals such as gallium, germanium, and antimony, which it possesses 80%, 60%, and over 50% of the world’s supply, respectively. While it is always possible to find other sources of critical minerals, it could take years to find a new source and establish a stable supply chain, like China’s predicament regarding its lack of advanced lithography equipment.
This has left many industries, especially those in the aerospace and defense sectors, feeling the heat of the trade war's results. The recent restrictions on antimony have caused significant concern among aerospace and defense original equipment manufacturers (OEMs), contract manufacturers (CMs), and electronic manufacturing service (EMS) providers.
Impact on Aerospace and Defense Companies
The aerospace and defense industries heavily rely on advanced and legacy semiconductors to power cutting-edge technologies and the minerals China has the lion’s share of. The ongoing trade war has had a massive effect on global aerospace and defense organizations. It will likely result in long-term impacts as OEMs, CMs, and EMS providers work to find alternative sources of chips and materials.
Increased costs and delays are some of the most significant disruptions the trade war can have on the aerospace and defense industry, which deals mainly with legacy components. Due to the global semiconductor shortage, aerospace and defense companies are already facing trouble with the increased likelihood of instances of obsolescence for these parts.
During the COVID-19 pandemic, these legacy components were less prioritized than the advanced parts that fueled consumer electronics, primarily used for remote work, which boomed during lockdowns. After the pandemic was mainly resolved, companies that had previously de-prioritized legacy components ceased production with no intention of returning them online.
Aerospace and defense OEMs, CMs, and EMS providers now have less availability of legacy components which come with higher costs and longer delays. China’s recent restrictions on antimony, a mineral used in “armor-piercing ammunition, night vision goggles, infrared sensors, bullets, precision optics, and the electronics industry, including semiconductors, cables, and batteries,” will further constrain this limited availability.
According to the Center for Strategic and International Studies (CSIS), “China is the world’s leading producer of antimony, accounting for 48% of global production and 63% of U.S. antimony imports. The likelihood of antimony supply disruptions has now increased significantly, necessitating the United States to quickly secure antimony supply chains from non-Chinese sources.”
The U.S. does not mine its own antimony, this began in 2001 after the shutdown of its Idaho mine. Recent restrictions on “six antimony products, including antimony ore, antimony metals, antimony oxide, and gold-antimony smelting and separation technologies " have resulted in an extreme increase in price.
“Prices have already doubled since the start of the year,” reports CSIS, “reaching an all-time high of $22,000 per metric ton. Some experts predict that prices could reach as high as $30,000 per metric ton as buyers stockpile and secure supply for future production.”
“China has already been cutting back on antimony exports for years as the country consumes more domestically…The latest export restrictions are only expected to widen the antimony market deficit, measured at 10,000 tons in May.”
Recently, legacy chips have begun holding more strategic value to countries due to their use in aerospace and defense systems. According to SEMI, 70% of all semiconductor production in 2022 came from South Korea, Taiwan, China, and Japan. For components that fall under the 50-to-180 nanometer range, China accounts for 30%, reports the Rhodium Group.
The Rhodium Group forecasts that China’s decision to become more self-sufficient could lead to China controlling 46% of the global capacity for 50-to-180nm chips within a decade, with China and Taiwan holding 80% of the 20-to-45nm foundry capacity within the next 3 to 5 years.
TrendForce adds that China’s mature-process capacity, “encompassing chips that are 28nm and above, is expected to grow from 29% to 33% by 2027.”
This could further restrict legacy components used by the aerospace and defense industries, weakening national security efforts and contributing to increased lead times and costs. Aerospace and defense companies must proactively mitigate these challenges before accessibility is further constrained by restrictions or other geopolitical volatility.
Long-Term Strategic Implications
Aerospace and defense OEMs, CMs, and EMS providers need to work toward forming solutions for these challenges now. The trade war between the U.S. and China shows no signs of slowing, and this year's coming elections might add more fuel to the already raging fire. Aerospace and defense companies must take proactive steps to achieve a more stable future supply chain.
Sustainable and Strategic Design Choices: One of the most critical steps aerospace and defense companies can take to mitigate the challenges of a heightened trade war is prioritizing sustainable and strategic choices within product development. This entails assessing the health of a product’s parts list or bill-of-materials (BOM), analyzing which components pose the most significant risk of unavailability, and replacing them with safer alternatives.
Similarly, organizations should identify which components have several form-fit-function (FFF) alternates, drop-in replacements (DIRs), or other functionally equivalent parts that can be used in case unavailability occurs at any point in a product’s life. Aerospace and defense companies make products that typically have long lifespans. As such, products should be developed in a way that can be repaired by anyone at any time.
Collaboration and Investment: Part of the reason original component manufacturers (OCMs) dropped specific legacy components from their production lines during the pandemic is the lack of financial feasibility to keep these lines in operation. Many legacy components, especially those that use more extensive processes, are cheaper than the cutting-edge semiconductors today. More affordable prices and low order amounts have led to many OCMs either dropping these components from their production or selling the legacy manufacturing equipment to other industries as it is more cost beneficial.
For aerospace and defense industries to ensure the availability of legacy components or other parts needed for their products, collaboration and shared investment in maintaining these lines must be made. The recent U.S. CHIPS Act is a way to help invest in maintaining component production necessary for aerospace and defense companies. The U.S. government has dedicated $35 million of its $52 billion program to chips for aerospace jets, specifically alongside a $162 million grant to Microchip Technology “to support its legacy chip-making efforts.”
Market Monitoring and Case Management: Due to the ongoing trade war and geopolitical realignment of the global semiconductor supply chain, components have a greater chance of becoming unavailable. The U.S. Department of Defense (DoD) has recognized the importance of semiconductors in the modern age and has developed practices to combat diminishing resources like chips. Following diminishing manufacturing sources and material shortages (DMSMS) guidelines, specifically SD-22, and SD-26, which provide methodology and steps to encourage and implement case management procedures to track progress efficiency effectively, is necessary for all aerospace and defense companies.
Furthermore, organizations can best plan on the likelihood of when case management is necessary by using market data to monitor component trends. Historical market analytics can help alert procurement teams to risky components as early as the development phase. For those components that can’t be avoided or replaced, case management can help provide a plan for the replacement of these parts.
The Trade War Has the Potential to Leave Long-Lasting Effects So Prepare Now
The U.S.-China trade war shows no signs of slowing. With the U.S. presidential election on the horizon, it could grow in severity depending on the newly elected administration. Aerospace and defense OEMs, CMs, and EMS providers face a new reality the longer these technologies and minerals are restricted. Increasing government intervention in the semiconductor supply chain will likely contribute to significant disruptions that could jeopardize national security.
Aerospace and defense organizations must be proactive rather than reactive to avoid these disruptions and mitigate the long-term effects. Investing in domestic OCMs to maintain component availability and replacing risky components with more stable parts is essential to developing more sustainable and strategic design choices.
Similarly, companies should invest in a market intelligence tool using predictive analytics to identify components prone to disruption or upcoming choke points. Sourceability’s market intelligence tool, Datalynq, can inform users of design risks associated with a specific part or BOM. This can help design engineers and procurement professionals gain greater supply chain visibility and make informed decisions regarding product development.
Datalynq is also integrated with Cadence’s OrCAD X Platform through Live BOM, providing users with real-time alerts to upcoming end-of-life (EOL), not recommended for new design (NRND), and other notices when issued. Sourceability experts can help you learn how to proactively leverage Datalynq’s scores to prepare for any challenge the trade war might create. Get started today with our experts here.
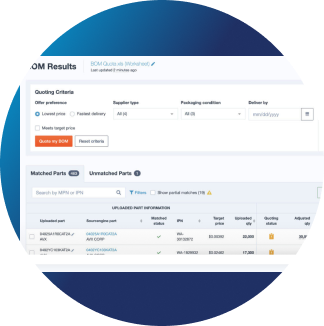
Quotengine: Your Ultimate BOM Tool
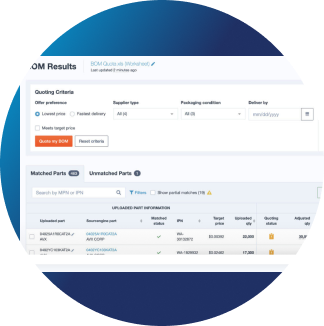
What’s Your Excess Worth?
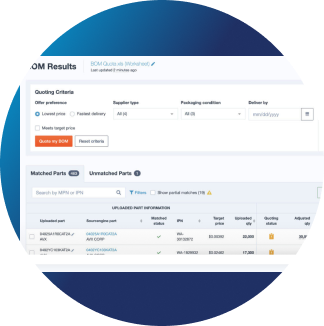
The Last Integration You’ll Ever Need
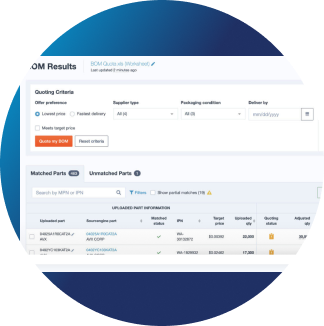
Sourcengine’s Lead Time Report
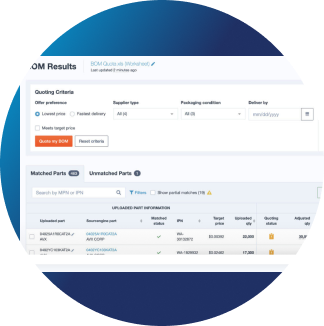
Sourcengine’s Lead Time Report
Your Lead Time Overview
Subscribe HereStruggling with excess inventory?
Download your free copy!.png)