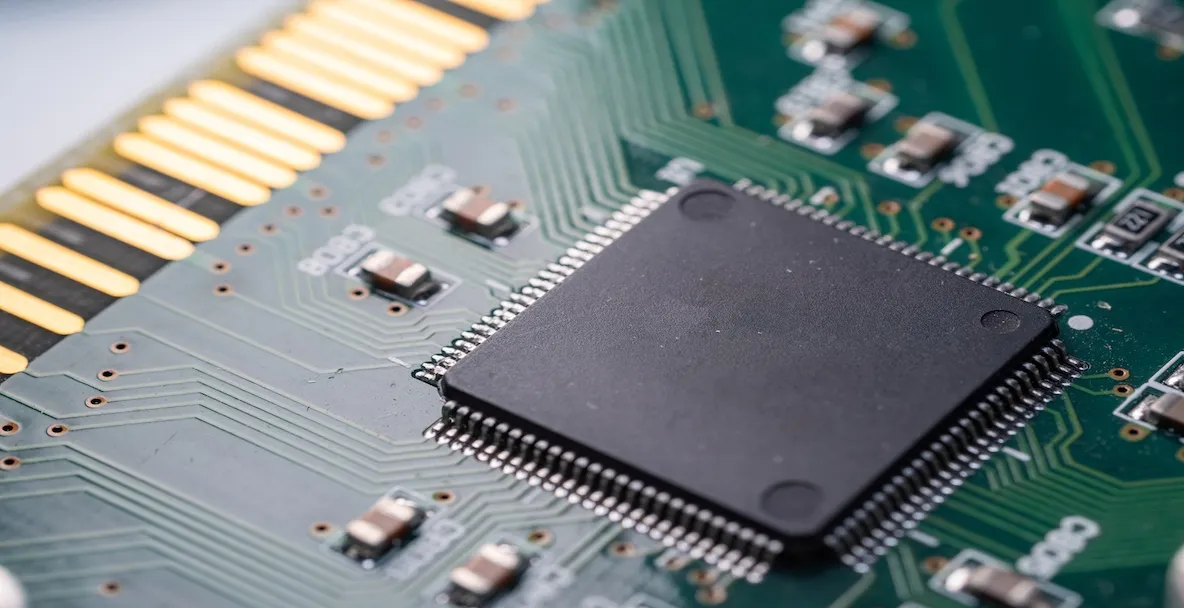
In the electronic components industry, component obsolescence is one of the most ever-present challenges that companies of all sizes grapple with. Component obsolescence is a complex issue that impacts every industry that relies on electronic parts, from consumer electronics to aerospace systems. Every organization will deal with obsolescence, from Tier 1 original component manufacturers (OCMs) to small electronic manufacturing service (EMS) providers.
Obsolescence has grown in severity in the last several years due to numerous factors. The rising rate of electronic obsolescence has contributed to significant disruptions across various sectors, leading to higher costs and extended lead times as organizations find alternate solutions. Obsolescence is expected to continue its upward growth in the coming years from the combined effect of the various factors contributing to its rise.
Understanding the cause of component obsolescence and its solutions is crucial for original equipment manufacturers (OEMs) and EMS providers, as it allows organizations to take proactive measures in strategizing for the eventual occurrence of obsolescence.
Why Obsolescence is Rising in the Electronics Components Industry
In the last several years, electronic component obsolescence has increased in frequency. One of the more troubling aspects of this increased rate of component obsolescence is instant obsolescence, or when a part enters obsolescence instantly without supplies for a last-time buy (LTB) or traditional end-of-life (EOL) transition.
With the introduction of artificial intelligence (AI) and the shrinking node size of advanced semiconductor processes, the rate of technological innovation has never been faster. As OCMs strive to create smaller, more efficient parts for AI applications, high-performance computing (HPC), hyperscale clouds, and more, older nodes are unable to compete and fall out of demand.
With fewer sales, OCMs are less inclined to continue producing previous generations. Similarly, advanced semiconductors have a shorter lifespan than older generations, significantly reducing the lifecycle for newer generations.
Ben Savage, Applications Engineer at Force Technologies Ltd., writes, “In 1970, the typical lifecycle of a semiconductor was expected to be about 30 years. By 2014, this was reduced to ten years—a 60% reduction in less than 50 years.”
Consumer demand plays a critical role in shaping the electronics industry. Demand for certain products and components wanes as trends evolve, making some components less financially feasible for OCMs and other chipmakers. For example, some chipmaking equipment that can only be used to manufacture legacy nodes, those 65 nanometers or larger, are more valuable to a chipmaker to sell than as a manufacturing tool.
Global semiconductor sales are typically dominated by communications or computer markets. The Semiconductor Industry Association (SIA)’s 2024 factbook reveals that in 2023, the lion’s share of chips was primarily procured for PC and communications segments, totaling 57% or $527 billion. Automotive and industrial sectors placed second at 17% and 14%, respectively. This is despite the significant drop in sales over the last year in response to the market downturn post-COVID.
For semiconductor fabs, production capacity is often determined by demand the year prior, with room for some margins if forecasts predict an upward or downward trend. If a component doesn’t have significant demand, capacity will be decreased. Since production capacity is limited, organizations might have to change their strategies if market demand rapidly fluctuates throughout the year.
This was seen throughout the semiconductor shortage during the COVID-19 pandemic when OCMs had maxed out their production capacity. OCMs had to prioritize their most lucrative lines, shutting down their less financially feasible operations. Once the shortage ended, many of these OCMs never restarted production for these components, instead taking them off their line cards and letting them enter instant obsolescence.
Furthermore, OCMs may push a component into EOL due to high production costs or trade restrictions, which strain the availability of raw materials. Without the materials readily available for component manufacturing, OCMs cannot continue their production. This could increase over the next four years as the U.S. President-elect, Donald Trump, takes office for a second term. The U.S.-China trade war as led to an increase in restrictions and heightened geopolitical tensions could see a rise in bans on critical materials necessary for semiconductor fabrication.
On a similar note, rising concerns regarding the environmental impact of semiconductor manufacturing have led to banning some materials deemed toxic for the environment. Growing efforts to comply with environmental regulations like RoHS (Restriction of Hazardous Substances) and WEEE (Waste Electrical and Electronic Equipment), will push for some components to become obsolete due to their hazardous manufacturing processes.
The Challenges of Obsolescence
Obsolescence presents a host of challenges for organizations across many industries. One of the most notable issues associated with component obsolescence is increased costs. This is due to a lack of availability leading to inflated prices, large LTBs, the cost of storing LTBs in properly maintained warehouses, and redesigns or recertifications for alternate components if no obsolete components are available on secondary markets.
During that time, finding and sourcing obsolete parts can contribute to supply chain disruptions, depending on what markets a company services. This can lead to longer lead times due to delayed production. These shortages can interrupt manufacturing schedules for other companies, possibly contributing to lost sales and a loss of vendor reputation among consumers.
Likewise, once a component enters obsolescence, technical support, documentation, or software updates are lost, making it more difficult for OEMs or EMS providers to troubleshoot challenges.
For some organizations, such as consumer electronics, it can be easier to handle obsolescence as there is a larger pool of OCMs and form-fit-function (FFF) alternates or drop-in replacements (DIRs) to substitute for the obsolete component. For high-reliability industries like healthcare, aerospace, and defense, LTBs are often the only solution, as even DIRs need to go through costly recertification processes to be cleared to go to market.
Similarly, when components enter obsolescence, stifled supplies become more constrained, contributing to greater component unavailability.
Solutions to Combat Obsolescence Challenges
Manufacturers and designers must take proactive measures to address the growing concern of obsolescence. The best way to start managing obsolescence is by prioritizing sustainability and strategic design choices via adopting a “right-to-repair” mindset. This means choosing components that have long-term availability, either through multiple manufacturers or having numerous active alternates, which is called multi-source availability. These widely available parts help reduce the impact of electronic component obsolescence.
Sole source components are parts that have no active alternates or other manufacturers. These parts can be incredibly detrimental to companies if they become obsolete because, aside from an LTB, there are no other sources or functionally equivalent parts that can be used to replace them. If a sole source component enters instant obsolescence, an organization has no other options beyond identifying and redesigning or sourcing obsolete stocks at a high price through spot buys.
To avoid the challenges associated with sole-source components, design engineers and procurement teams must work together to understand which parts pose such risks and remove them from a product’s bill of materials (BOM). Design teams should replace sole sources with parts that have greater multi-source availability, making them more sustainable in the long term.
Concurrently, organizations should take a proactive approach to structured lifecycle management, identifying potential risks early and utilizing case management procedures that plan to address issues long before obsolescence occurs. The U.S. Department of Defense’s Diminishing Manufacturing Sources and Material Shortages (DMSMS) guidelines offer stringent guidelines on managing cases that arise from component unavailability for any reason, like obsolescence.
The methodology offered within the DMSMS applies not only to high-reliability industries such as defense and aerospace but can also be used by OEMs and EMS providers within consumer industries to help prepare for obsolescence.
Finally, using a market intelligence tool that provides insights into the risks associated with specific electronic components, such as sole source status, can help engineers and procurement teams remain aware of a component's lifecycle at any point.
By anticipating future obsolescence through market intelligence tools, organizations can avoid potential disruptions and plan for cost-effective replacements. Due to increasing factors, electronic component obsolescence may have increased over the last several years. Still, taking these steps is not a highly complex and costly problem.
Proactive Steps to Managing Obsolescence
Obsolescence is increasing due to the fast-moving pace of the electronics industry. Driven by technological advancements, shifting market demands, and financial feasibility, many electronic components are expected to enter EOL within the coming years. However, the costly effects of obsolescence can be successfully managed with proactive lifecycle management that is accomplished through sustainable and strategic design choices, stringent case management procedures, and market intelligence tools.
By addressing obsolescence head-on, companies can safeguard their supply chains against delayed production, lost sales, and costly redesigns while ensuring the long-term viability of their products.
Sourceability works with a team of supply chain experts and procurement professionals who utilize our leading-edge digital tools to help clients identify challenges and lower the risks associated with obsolescence before they occur. For organizations that need help sourcing components with greater multi-source availability, Sourceability can identify less risk-prone parts that clients can procure through our global e-commerce platform, Sourcengine.
Likewise, Sourceability’s market intelligence tool, Datalynq, can help organizations begin cases for unavoidable sole-source parts and aid businesses in predicting when components are more likely to become unavailable during supply chain disruptions. Reach out to our experts today to prepare for the rising tide of obsolescence.
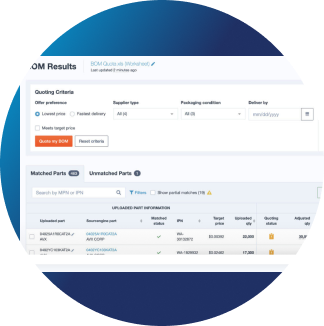
Quotengine: Your Ultimate BOM Tool
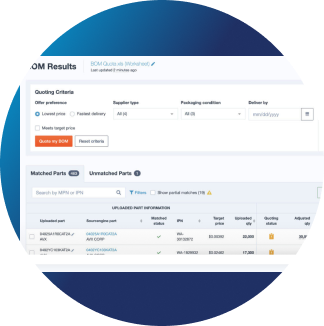
What’s Your Excess Worth?
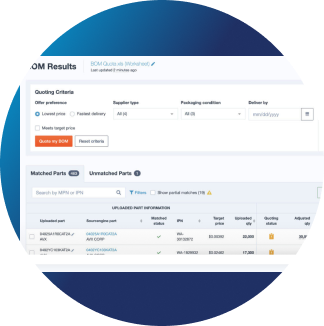
The Last Integration You’ll Ever Need
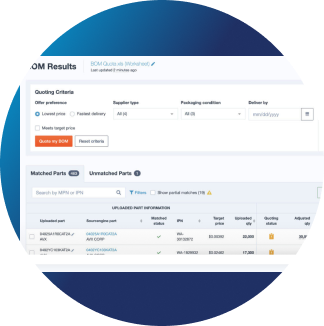
Sourcengine’s Lead Time Report
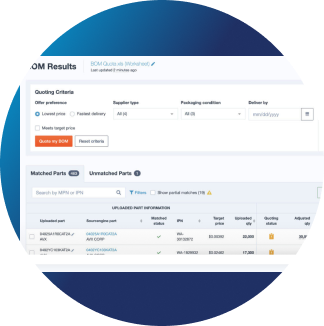
Sourcengine’s Lead Time Report
Your Lead Time Overview
Subscribe HereStruggling with excess inventory?
Download your free copy!.png)