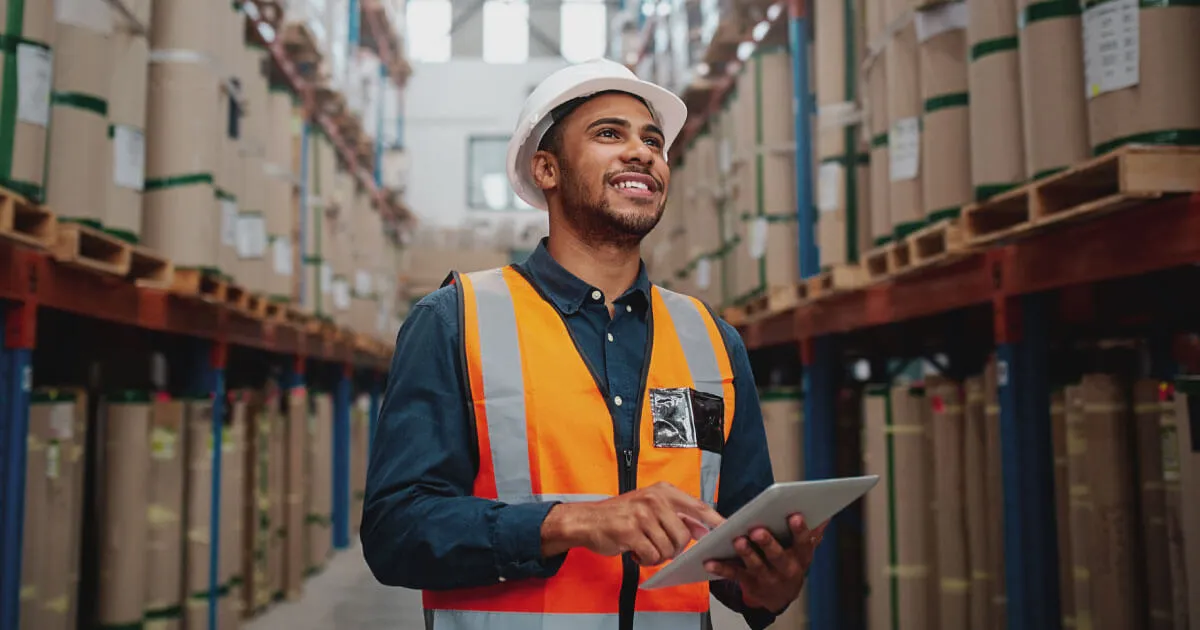
For electronics manufacturers, the coronavirus pandemic has had a similar impact to a natural disaster. The outbreak happened suddenly, inflicted severe widespread damage, and inspired significant uncertainty about the future. But with time, organizations have begun to recover, and analysts are drawing lessons from all that has happened.
Recently, consultant group Bain & Company published a report about the crisis’s effect on international production and logistics which helps companies understand its deep impact.
Here are three things original equipment manufacturers (OEMs) and contract manufacturers (CMs) should know about the post-pandemic global supply chain.
The Coronavirus Has Reshaped Supply Chain Risk Management
One of the key observations Bain & Company's report makes about the current landscape is that manufacturers should revise their understanding of supply chain risk management. In the past, OEMs and CMs thrived by working with the same vendors, shipment companies, and distributors. The industry can be very relational based. The occasional disruptive event would cause problems, but established operating methodologies worked well enough to preclude any major changes.
However, the 21st century quickly rendered decades of traditional wisdom and practice obsolete. Unforeseen events like the 2010 Icelandic volcano eruptions, the 2016 earthquakes in Kumamoto, Japan, Brexit, and the U.S.-China trade war have highlighted the drawbacks of a global supply chain. Firms had previously found great success in cutting cots by outsourcing labor and manufacturing. But now those practices have become a liability when companies temporarily lose access to their main suppliers.
Though the risk exposure inherent to the global supply chain has long been evident, the pandemic revealed the devastating consequences of not addressing the vulnerability. OEMs and CMs suffered from shipping cost hikes, component shortages, and limited logistics visibility. Conditions have since normalized, to an extent, but the takeaway is clear: the old ways of doing things are not fit for purpose in “the new normal.”
As such, manufacturers need to rethink their established procedures and develop new methodologies to ensure continued success.
Supply Chain Resiliency Protects OEMs
Bain concluded manufacturers can best protect themselves from unpredictable calamities by making their supply chains more resilient. The process is multifaceted, but it involves vendor diversification, forging closer relationships within the supply chain ecosystem, and increased technological integration (the key element).
By establishing a range of primary and alternate suppliers, firms can ensure their teams have the necessary components for projects, even in the middle of a world-shaking event. When brands share information with their suppliers, logistics partners, and distributors, OEMs, and CMs gain a much greater level of supply chain visibility. Most importantly, manufacturers become considerably more agile after digitizing their operations.
Enterprise resource management (ERP) software gives companies the ability to react quickly to standard volatility and new disruptions. Manufacturers can use data provided by their partners to anticipate part shortages and shipping delays via artificial intelligence enhanced risk scenario modeling. Cutting-edge digital platforms also enable OEMs and CMs to adjust their operations to compensate for unforeseen and mission-critical problems.
For example, Sourcengine’s BOM Tool allows supply chain professionals to order electronic components from thousands of traceable vendors while providing unprecedented price comparison. Such a tool helps brands tackle issues like unexpected component needs when the typical supply chain route is cut off. In such an event, this tool can help procure necessary components by opening up new relations and supply chain route options through BOM management options.
Digitization Drives Financial Growth
Bain & Company's recommendation that manufacturers make supply chains more resilient is not just about preparing for the worst. The firm’s analysis reveals that companies can experience meaningful financial growth after digitizing their operations.
The consultancy notes its clients reduced their product development cycles by up to 60 percent because design teams could adjust to changes in market preferences more quickly. The firm also states brands with flexible supply chains improved their output capacity by 15 to 25 percent. The group also found that manufacturers increased inventory turn and customer satisfaction rates by as much as 40 percent post-technological integration.
OEMs and CMs can enjoy these benefits because supply chain digitization allows them to move faster, reduce inefficiencies, and bolster sales. With TrendForce recently predicting a near-term decline in global electronics demand, firms cannot afford to live in the past.
The True Meaning of Resiliency
Ultimately, resiliency is not about how quickly an organization reacts to disaster. It is about emerging from periods of adversity stronger, smarter, and better than they were before. For electronics manufacturers, this means not only rebounding from the coronavirus pandemic, but doing so in a manner that brings true development to procurement processes and strategies.
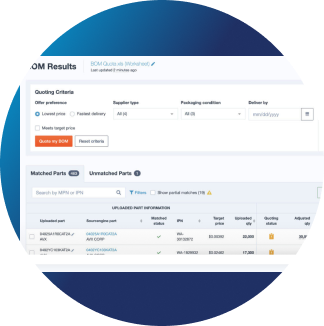
Quotengine: Your Ultimate BOM Tool
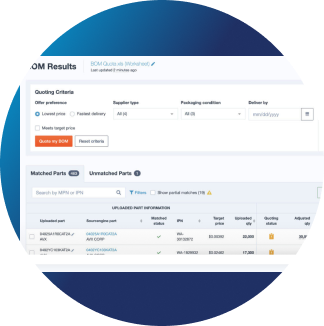
What’s Your Excess Worth?
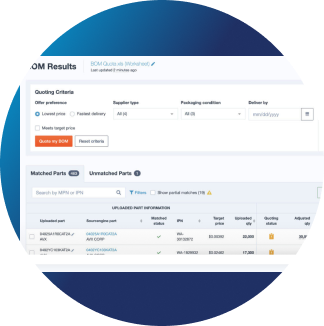
The Last Integration You’ll Ever Need
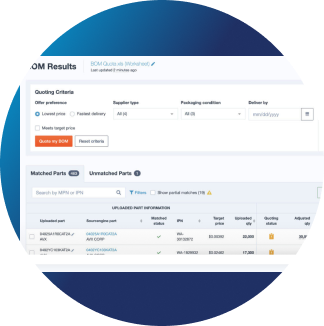
Sourcengine’s Lead Time Report
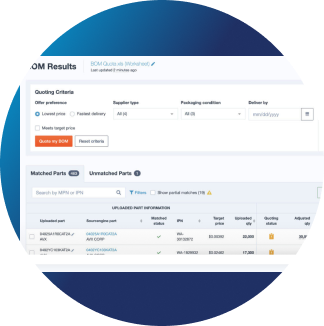
Sourcengine’s Lead Time Report
Your Lead Time Overview
Subscribe HereStruggling with excess inventory?
Download your free copy!.png)