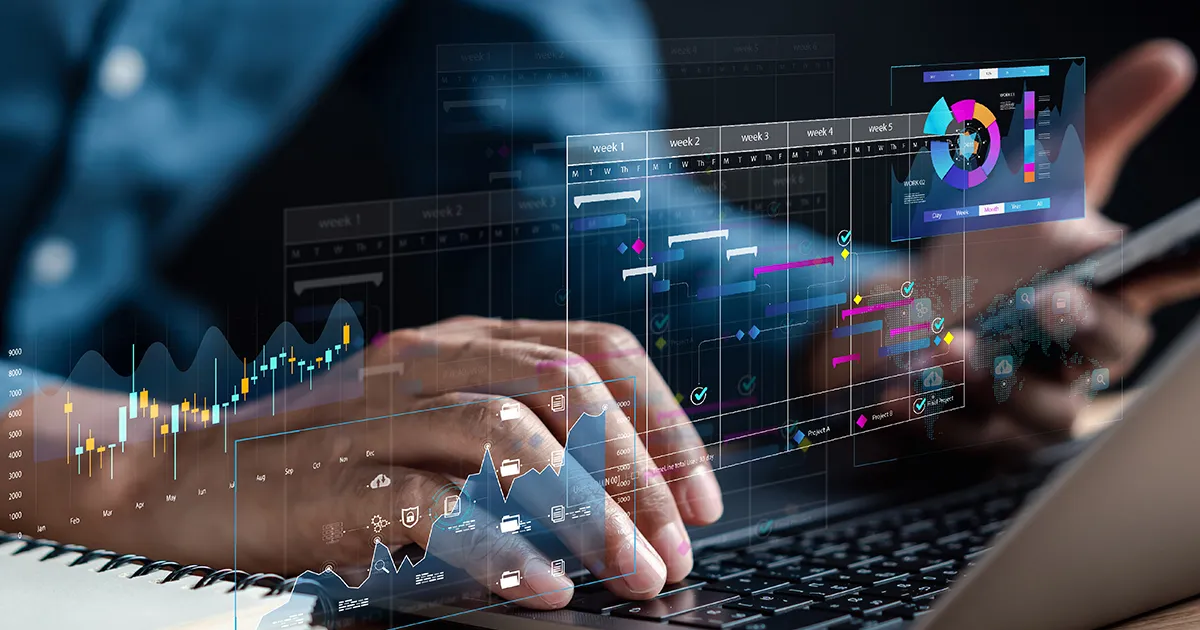
Within manufacturing, there is one critical piece of data that ensures production runs smoothly. It is a parts list or bill of materials (BOM). A BOM is the extensive list of raw materials, electronic components, and sometimes instructions required to construct, manufacture, or repair a product or service. For original equipment manufacturers (OEMs), contract manufacturers (CMs), electronic manufacturing service (EMS) providers, and others, a well-structured and detailed BOM is critical.
A well-formed BOM is necessary for electronics manufacturers as it aids in providing details for engineering processes, advanced product lifecycle management (PLM), and manufacturing processes. It is the foundation of any product or service’s manufacturing process to move a product from the design phase to reality.
The primary purpose of a BOM is to create the most straightforward and accurate digital representation of a product so that any team within the organization, from engineering to purchasing to sales, can understand what a product offers. A bill of materials shows the relationship between the finished product and its components. It helps estimate the cost of materials, plan purchases, ensure the availability of parts, and avoid production delays. For procurement teams, BOM management goes more smoothly the more detailed a BOM is.
Not all BOMs are created equal. There are different types of BOMs that suit specific situations or are better fitted to various industries. BOMs for electronic components must be highly specific to aid procurement teams in navigating the often-complicated global supply chain.
BOM Types
At its core, a BOM is necessary for building a product, ordering replacement parts, and reducing future issues if repairs are required. A detailed and structured BOM helps purchasing teams plan for the acquisition of orders and streamline the procurement process. Two basic types of BOMs are utilized within the electronic component industry: engineering BOMs and manufacturing BOMs.
The Engineering BOM
An engineering BOM (or EBOM) defines the design of the completed project while including alternative or equivalent parts in the drawing notes. Every line within an engineering BOM has a product code, part name, part number, part revision, description, quantity, unit of measure, size, length, weight, and product specifications or features. Engineering BOMs are most often organized and created through computer-aided design (CAD) drawing programs. Multiple engineering BOMs might be created for a finished product from redesigns or other phases during product lifecycle management.
The Manufacturing BOM
A manufacturing BOM (or MBOM) details the assemblies and parts required to construct a finished item for shipment. Manufacturing BOMs usually require packaging materials necessary to send a product to a customer alongside the required execution of the product before completion. A manufacturing BOM typically stores all the information required for manufacturing activities. OEMs, CMs, or EMS providers on the production line usually utilize these BOMs in-house.
The engineering BOM is the most commonly used type of BOM within the electronic component industry, especially by procurement teams. There are several other types of BOMs beyond manufacturing and engineering, such as sales, configurable, assembly, and more. However, for electronic component procurement, EBOMs are the most utilized. Furthermore, it is their sublevels or subassemblies that contribute to the success of the project’s production and the procurement process.
Understanding BOM Levels
For most engineering and manufacturing BOMs, the production process for a single product is complex and dimensional. To accurately define the necessary components for a product and its subassemblies a multilevel BOM is necessary.
A multilevel BOM, or an indented bill of materials, is “a hierarchical structure representing the components, subassemblies, and finished products required to manufacture a particular item.” This gives manufacturers and procurement teams a comprehensive view of the product’s complete manufacturing process. Simply, it breaks down everything needed for the product to be considered finished.
The purpose of a multilevel BOM serves two main functions within the manufacturing process. Firstly, it gives an overview of assemblies which possesses greater detail and specificity on the subassemblies within the product and the relationship between them. Secondly, it further decreases the chance of errors when interacting with subassemblies through structured documentation that helps organizations more accurately track parts.
A multilevel BOM can have as many levels as a product requires. For example, an office chair possesses a multilevel BOM which is broken down into these levels. The first level is the chair itself as the finished product. The second level are the main components such as the seat cushion, chair’s frame, the wheels, and so on. The third level would go into further detail regarding the subassemblies of each main component, which would be the nuts, bolts, and frame materials needed to create the chair frame itself.
One can imagine how complex a multilevel BOM becomes when electronic components are involved. Especially when trying to maintain such a BOM through traditional tools that are improperly equipped to handle the significant size of large BOMs, like Excel. This often leads to various errors compromising the accuracy of the presented data.
While some industries can utilize single-level BOMs that don’t have the same depth and detail as multilevel ones, for any technology integrated projects the latter is extremely pertinent to both manufacturing and procurement.
What Procurement Teams Need from a BOM
BOMs are advantageous to organizations because they can streamline the manufacturing process and improve efficiency through their detailed structure. BOM management processes can help further reduce waste by identifying the amount of required stock, highlighting vulnerabilities via sole source components, and aiding organizations in strategizing future deliveries to avoid supply chain disruptions.
An engineering BOM is necessary for electronic component purchasing teams thanks to their comprehensive coverage of component and material details. To best aid procurement teams, a BOM should include manufacturer part numbers (MPNs), product names, part descriptions, unit costs, form-fit-function (FFF) alternates or drop-in replacements (DIR), part quantities, and manufacturer names.
This information aids procurement teams exponentially in searching for and locating suppliers that can adequately distribute the electronic component stock at a reasonable price. Likewise, including alternates helps prevent future challenges and delays should a component enter obsolescence or be otherwise unavailable due to various factors. Organizations can more effectively save on operational costs by preventing inventory or production delays through aggressive BOM management practices such as BOM scrubbing.
One can best accomplish these tasks through the aid of a digital BOM management tool that can instantly present real-time market offers, component alternates, and a simple check-out process.
Quotengine is the BOM Tool for
Quotengine is a digital BOM management tool for any sized OEMs, CMs, EMS providers, and more. Integrated with the leading e-commerce site for electronic components worldwide, Sourcengine, Quotengine can quickly fetch part offers for components on your BOM list that best fulfill your requirements. With its enterprise quoting feature, users can add up to 4,000 line items per BOM with the ability to filter through offers to find the perfect match.
With Quotengine, procurement teams can effectively and quickly compare part offers without using multiple tabs, dozens of Excel sheets, or long phone calls with sales representatives. Quotengine users can upload their BOM for instant offers with the ability to add all or select specific offers to the cart for one quick transaction. If needed, each part contains additional information, including lead times, compliance data, FFF alternates, and component technical data.
Quotengine allows users to share offers or their cart with other members within your organization and team. This lets users gain approval from upper management before committing to a required purchase. Order history is stored on Sourcengine so users can quickly reorder past BOMs if necessary. Users can schedule deliveries up to 12 months in advance to keep production lines moving.
The electronic component industry is complicated, and the BOMs utilized to make the products within it even more so. With innovative BOM management tools like Quotengine, these challenges are no longer a problem.
Ready to get started? You can upload your BOM and start using Quotengine now. Additionally, for those struggling with excess electronic component inventory, you can now estimate your maximum return for selling excess on Sourcengine through Quotengine’s platform. Try it out today for no cost!
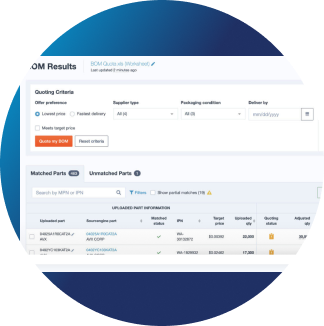
Quotengine: Your Ultimate BOM Tool
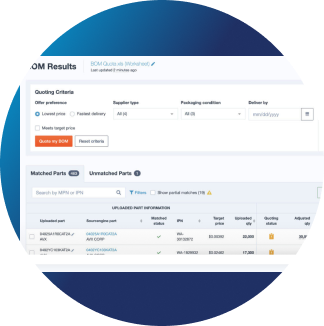
What’s Your Excess Worth?
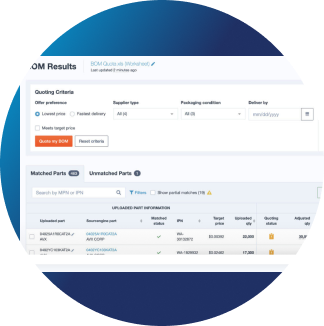
The Last Integration You’ll Ever Need
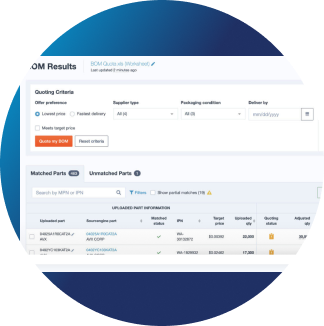
Sourcengine’s Lead Time Report
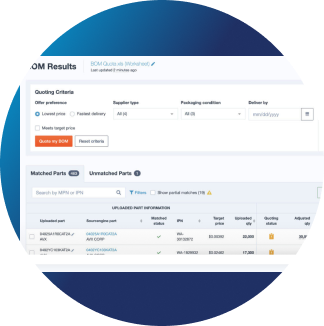
Sourcengine’s Lead Time Report
Your Lead Time Overview
Subscribe HereStruggling with excess inventory?
Download your free copy!.png)