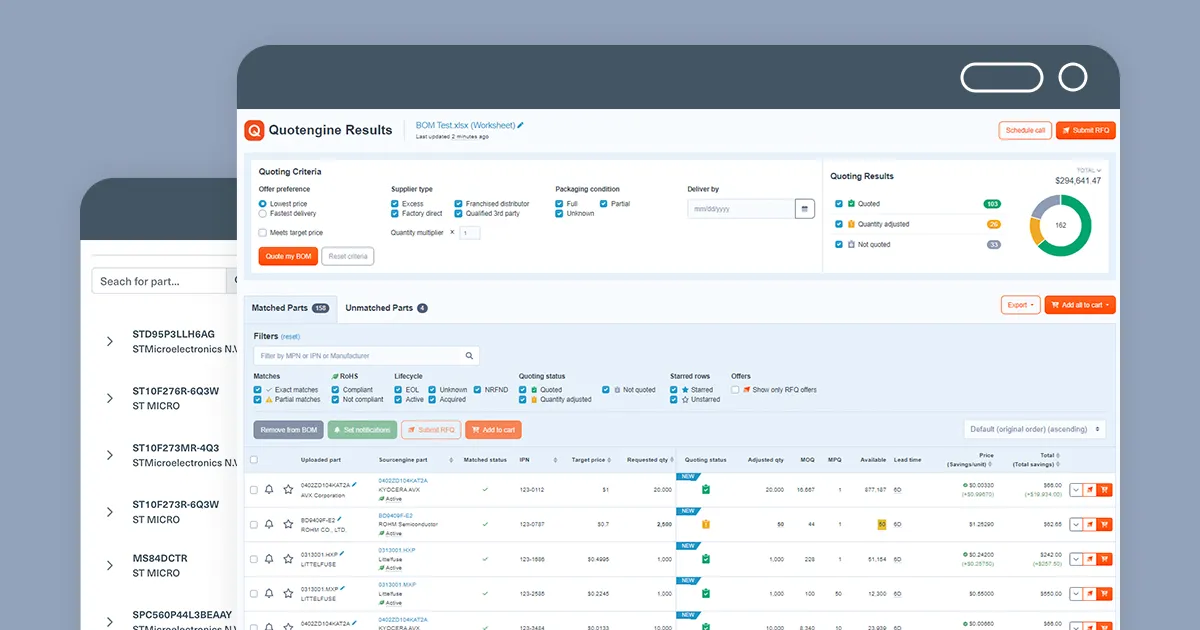
One of the most important aspects of electronic component procurement is a bill-of-materials (BOM) or parts list. A BOM is a necessary guide for both engineering and purchasing teams as it documents the electronic components that make up a product for future reference, and it, in a nutshell, is a shopping list for buyers to refer to quickly. That said, there is much more to a BOM than just a list containing the necessary project parts.
A BOM helps improve manufacturing accuracy and efficiency. The more detailed a BOM is, with manufacturing part numbers (MPNs) and comprehensive part data, the more it can help streamline future operations. That, however, only works if the information is indeed accurate.
To err is human; manually inputted information can be prone to inaccurate data and other inconsistencies. Should a BOM possess such errors or lack proper information, it could complicate the manufacturing process and create challenges that need time and capital to resolve. To prevent human error or other invalid information from appearing on your BOMs, it is imperative to partake in BOM scrubbing.
What is BOM Scrubbing?
BOM scrubbing scans a BOM or parts list to resolve any inconsistencies, errors, or potential risks by ensuring the data, such as part numbers, are correct and accurate. It relies on collaboration between program managers and buyers to properly align a customer’s order with a manufacturer’s capabilities. Within manufacturing, BOM scrubbing is essential to ensure efficiency and accuracy.
Overall, the process of BOM scrubbing is relatively simple. It ensures a BOM is correct, authentic, and available by checking the listed data within your enterprise managing system (ERP) or other numbering systems. Doing so prevents delays and allows for proper quoting on future projects. One must complete several necessary steps for a comprehensive BOM scrub.
Proper MPN and Part Data: With long and often complex MPNs, it is easy for anyone to accidentally mix up an O and 0 or miss a dash or a letter. To ensure accuracy, check all MPNs against your numbering system or utilize a global electronic component e-commerce site integrated with an extensive PCB CAD library. This way, one can quickly identify and replace inaccurate MPNs with proper ones.
Also, a detailed component description alongside an MPN can help teams scrubbing a BOM to identify the correct MPN should an inaccurate number be listed. If part data sheets are unavailable, creating a clear description that includes part type, size, speed, etc. should be included.
Identify and Mitigate Risks: To prevent delays and other disruptions from impacting your manufacturing process, removing risky parts from a BOM before reaching your procurement team can make a difference. This means checking for the parts that are not recommended for new design (NRND), end-of-life (EOL), last-time-buy (LTB), obsolete, discontinued, or counterfeit.
Other risky component types that should be removed from your BOM are sole source components. These components are classified as sole source by having no form-fit-function (FFF) or functionally equivalent alternates, not being manufactured by multiple original component manufacturers (OCMs), and possessing no active alternates. Should a sole source component become unavailable, there will be no possibility of recourse leading to delays or, worse, costly redesigns.
A market intelligence tool, such as Datalynq, can help users locate and remove sole source components before problems arise. Other risk-identifying scores, such as multi-source availability and design risk, help users quickly identify and remove other concerning parts instead of manually checking each.
Vendor Verification: Quality is among the most critical things in the electronic component industry. The global semiconductor shortage gave rise to a variety of bad actors that are known to target any and all manufacturers if they are in desperate need. While many experts believe you should only purchase components directly from the supplier, that is not always possible with the number of components rising in use.
During BOM scrubbing, it is vital to ensure that components are purchased from verified and traceable suppliers or through a distributor that is ISO 9001 certified and implements an aggressive quality management system (QMS) based on ISO guidelines. This lowers the risk of counterfeit components entering your supply chain and causing further delays and malfunctioning equipment should they possibly enter your production line.
Find and Include Alternates: One of the most important steps during a BOM scrub is locating equivalent electronic components, form-fit-function (FFF) alternates, or drop-in replacements (DIR) for components that are either shortage-prone or facing future obsolescence. By having alternates on your BOM for the main electronic component, you are proactively preparing for problems long before they arise. That lowers the possibility of delays impacting your production line when attempting to find the right cross.
Now, all these steps may sound like a lot of effort, and if done manually, it can be. It is necessary as it helps fortify BOMs and the manufacturing process itself. Unfortunately, an effective BOM scrub is often ignored due to time constraints and the lack of devoted staff to analyze a parts list.
Thankfully, there are tools to aid teams in successfully managing and scrubbing their BOMs without losing time or capital.
Quotengine and Datalynq
Digital BOM management tools help manufacturers save time and cost and prevent production delays. Datalynq, a market intelligence tool, lets users upload their BOMs for proper analysis, alerting users to severe risks through its real-time electronic components market data. Using information from Sourcengine, one of the largest e-commerce platforms for electronic components, Datalynq presents easy-to-read scores on design risk, multi-source availability, market availability, inventory trend, and price.
Each component is given a score from 1-to-5 in these areas giving users a comprehensive view of the possible benefits and challenges associated with a part. The multi-source availability score alerts users to the likelihood of a particular component being sole source, allowing engineers to remove it from a product before problems arise.
Once the risks associated with a BOM are successfully mitigated through Datalynq, users can upload their scrubbed BOM into Quotengine to find filter offers that best fit a manufacturer’s need. Since Quotengine is integrated with Sourcengine, users can be assured the components purchased through the site are quality thanks to the stringent QMS process all stock must go through. Users can share their uploaded BOM alongside listed offers, and part alternates to other members of their organization for a second-verification process if needed.
Accomplishing a successful and effective BOM scrub is easy with digital tools like Quotengine and Datalynq. Today, you can scrub your BOM for risks and errors to improve your procurement process.
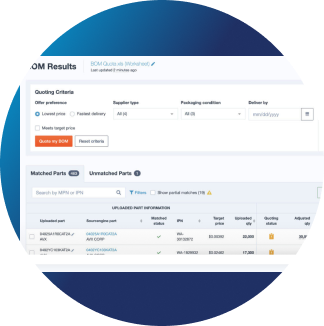
Quotengine: Your Ultimate BOM Tool
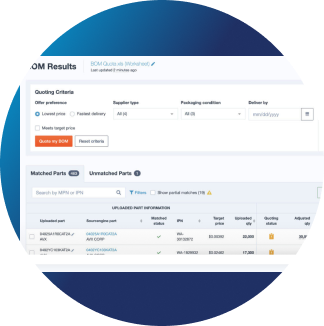
What’s Your Excess Worth?
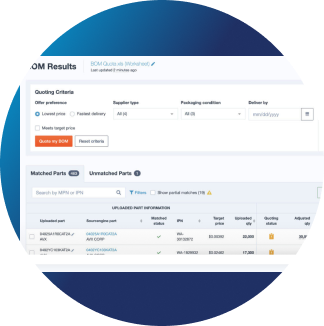
The Last Integration You’ll Ever Need
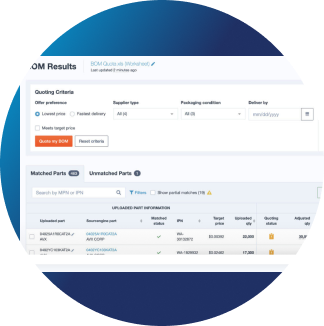
Sourcengine’s Lead Time Report
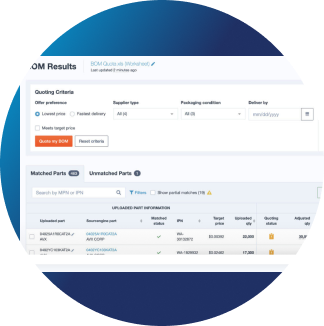
Sourcengine’s Lead Time Report
Your Lead Time Overview
Subscribe HereStruggling with excess inventory?
Download your free copy!.png)